is a ferritic iron-chromium-aluminum alloy tube (FeCrAlMo Alloy) manufactured by advanced powder metallurgical technology, with high thermal conductivity, high mechanical strength, and excellent high temperature corrosion resistance, can withstand prolonged temperature up to 1250 ° C (2280 °F).
APMT offers design engineers better options in the applications that were previously considered to be the domain of ceramic materials, and solves the problems of conventional nickel based alloys. Whether you are a furnace builder, burner manufacturer, or a user of a furnace suffering from performance limitations, or requiring heavy and regular maintenance, APMT just may be the problem solver you have been waiting for.
Superior oxidation properties, sagging problem solution
Alumina forming alloys have long been known to possess superior resistance to oxidation as compared to conventional chromia forming NiCr, and FeNiCr based alloys.
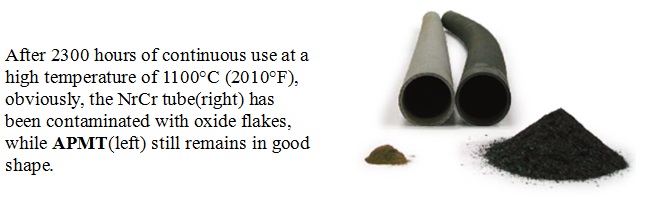
Clean and maintenance free in operation
The protective alumina film resists spalling during thermal cycling, thus will not contaminate products in the furnace, or cause electrical short circuits in any heating elements installed inside APMT protection tubes. APMT require no maintenance during operation, which means fewer production stoppages.
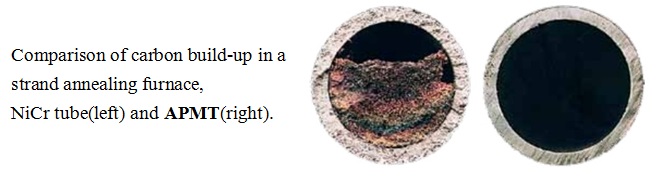
APPLICATIONS
Used mainly in the heat treatment, steel and aluminum industries, typical applications for APM are as radiant tubes in electrically or gas fired furnaces such as continuous annealing and galvanizing furnaces, seal quench furnaces, holding furnaces and dosing furnaces in the aluminium, zinc, lead industries, thermocouple protection tubes, furnace muffles for sintering applications.
Outstanding Protection tubes for thermocouples
APMT alloys have a long record of successful installation as protective tubes for thermocouples up to temperatures of 1250° C. There are also some installations where tubes have been used up to 1400° C, after special design considerations.
The advantages offered by using APMT:
- High resistance to attack by sulphur compounds and to carburization.
- The high temperature resistance of the material makes it possible to produce tubes with thin walls with a long service life. Thin walls give rapid heat transmission, which means higher sensitivity to temperature variations.
- The aluminum oxide layer on the protection tube has a minimal tendency to spall, which means that contamination is avoided.
- No risk of short-circuiting caused by spalled oxide. In contrast to chromium oxide, aluminum oxide is not electrically conductive.
Contact us for more product information.
|